2段ユニットを1度に吊り込む
まず建物外部ヤードにて、下部の図のようなユニットを作ります(図2)。それをフォークリフトで2段重ねてストックしておき、2段のまま設置場所に吊り込みます。
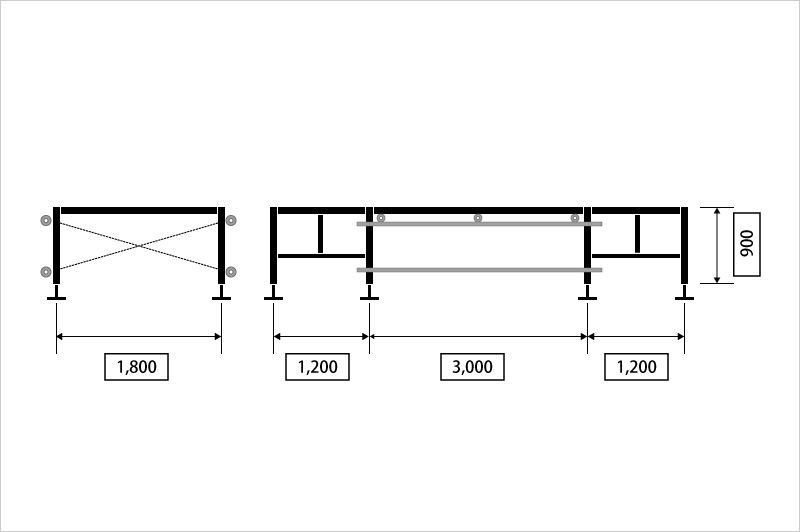
【図2】建物外部ヤードで作ったユニット
このユニットは、全体の3分の1の数(120基)ほど作って、梁底の型枠施工後に吊り込みました。
2段のまま吊り込んだユニットですが、上の1ユニットは、吊り直して隣りへ移動します(図3)。
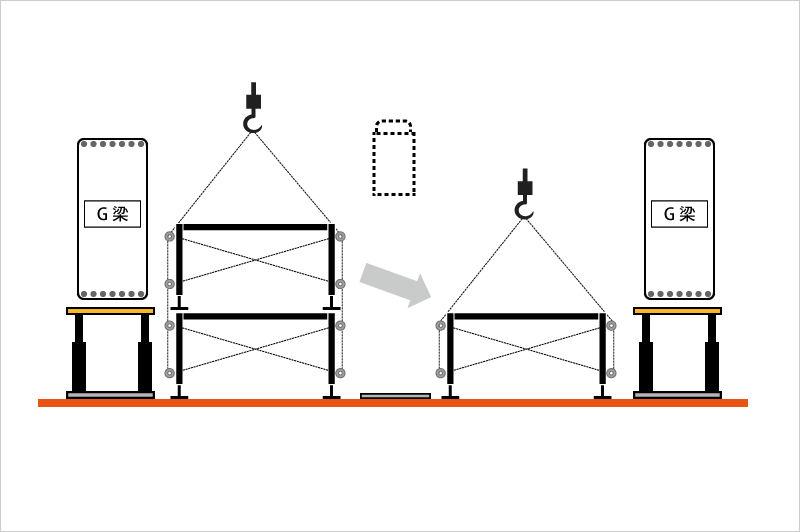
【図3】2段で吊り込んで上のユニットを隣へ移動する
そして、2つのユニット間を移動可能にするために、両サイドに渡りを設けました(図4)。
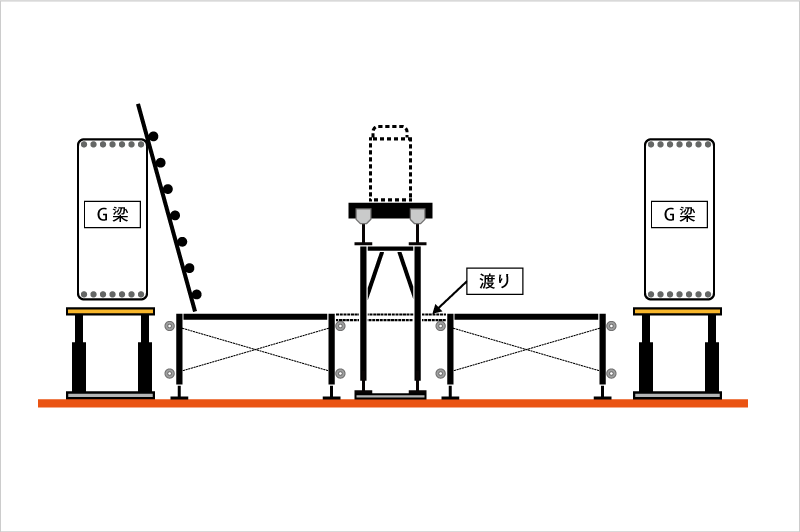
【図4】ユニット間に渡りを設ける
これによりマスの中を自由に移動できる形状になります。足場がフラットで手摺りもないため、鉄筋のフープや型枠の資材を仮置きできるようになり、作業効率が大幅にアップしました。
※中央部分には、後にPC梁が乗るW=600、L=1200×2スパンの枠組みの支保工が入るため後施。
必要人工を在来工法の4分の1に削減
G梁の配筋が始まると、鉄筋のフープをはじめ、小物を置くスペースがたくさん確保でき、配筋作業が安全かつスムーズになりました。型枠工事も、同様に安全かつスムーズに進みました。
一般的な工法は、(1)足場資材の取り込み、(2)足場の組立て、(3)余った資材の回収といったように、かなりの時間と手間がかかります。解体時も同様です。
それに比べ、この建物の外部で足場のユニットを組み、短時間で吊り込む方法は、建物内の作業を邪魔することなく、とても効率的です。
次のユニットが吊り込まれる間に、渡り部分を施工することもでき、残材もゼロ。結果、足場の吊り込みから完成まで、鳶3人で作業でき、半日強で12スパン、24基を設置できました。この2段ユニットを1度に吊り込み、上のユニットを隣へ降ろす画期的方法によって、かかった人工は、在来工法と比較すると4分の1になりました。
ユニット化した足場を繰り返し利用
型枠を施工した後は、PC梁のセット、デッキプレートの敷き込みとなりますが(図5)、PC梁のセットが終わった時点で中の足場は、吊り込みの逆の手順で、隣の工区に移動し設置します。
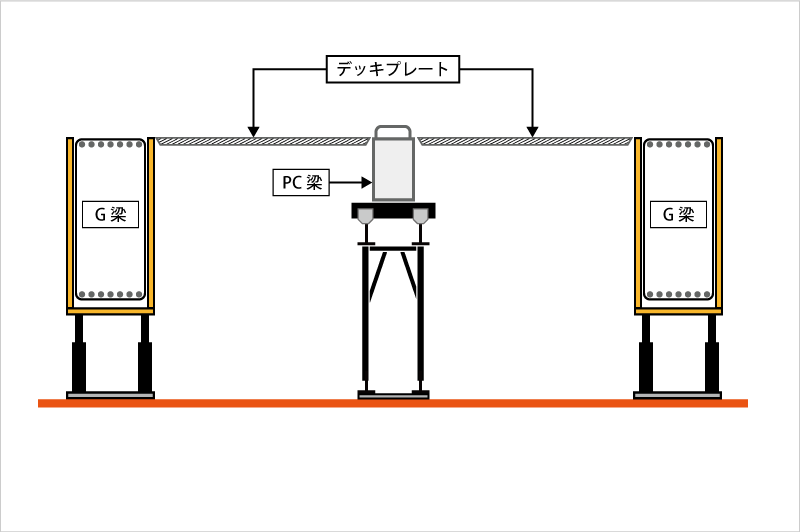
【図5】型枠施工後、PC梁のセット、デッキプレートの敷き込みを行う
この手順により、ユニット化した足場を繰り返し利用することが可能になり、短時間での足場の設置が可能となりました。
以上、資材の出し入れの時間や、クレーンの使用時間など、在来工法では考えられない、想像以上の施工効率化を実現したアイディア事例でした。一つとして同じ現場はありませんが、新たな発想につながれば幸いです。